Les méthodes de revêtement de résine photosensible sont généralement divisées en revêtement par centrifugation, revêtement par immersion et revêtement au rouleau, parmi lesquels le revêtement par centrifugation est le plus couramment utilisé. Par revêtement par centrifugation, la résine photosensible s'égoutte sur le substrat, et le substrat peut tourner à grande vitesse pour obtenir un film photorésistant. Après cela, un film solide peut être obtenu en le chauffant sur une plaque chauffante. Le revêtement par rotation convient au revêtement de films ultra-fins (environ 20 nm) jusqu'à des films épais d'environ 100 um. Ses caractéristiques sont une bonne uniformité, une épaisseur de film uniforme entre les tranches, peu de défauts, etc., et un film avec des performances de revêtement élevées peut être obtenu.
Processus de revêtement par rotation
Lors du revêtement par rotation, la vitesse de rotation principale du substrat détermine l'épaisseur du film de la résine photosensible. La relation entre la vitesse de rotation et l’épaisseur du film est la suivante :
Spin=kTn
Dans la formule, Spin est la vitesse de rotation ; T est l'épaisseur du film ; k et n sont des constantes.
Facteurs affectant le processus de revêtement par centrifugation
Bien que l'épaisseur du film soit déterminée par la vitesse de rotation principale, elle est également liée à la température ambiante, à l'humidité, à la viscosité et au type de photorésist. La comparaison des différents types de courbes de revêtement de résine photosensible est présentée à la figure 1.
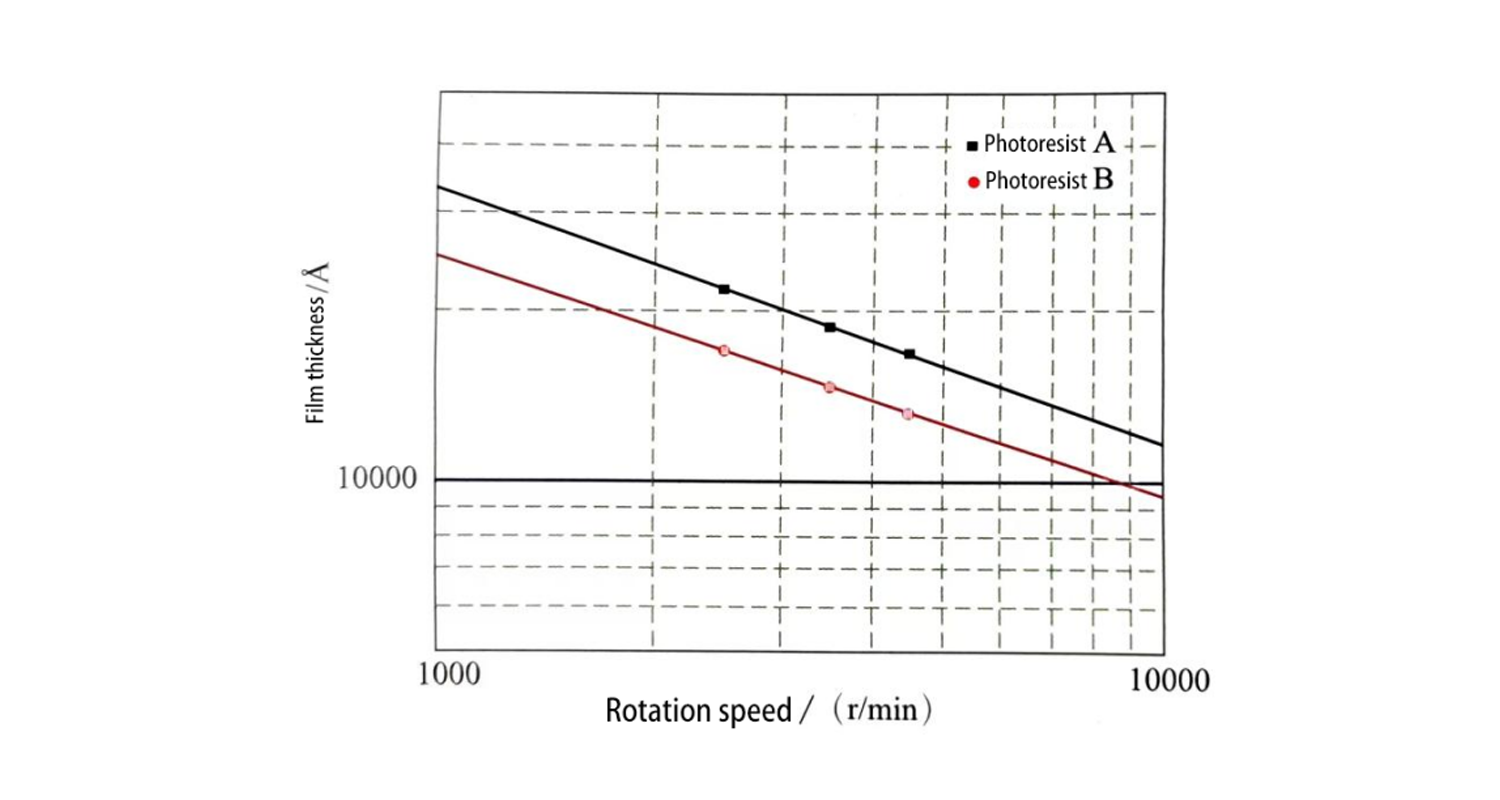
Figure 1 : Comparaison de différents types de courbes de revêtement de résine photosensible
L'influence du temps de rotation principal
Plus le temps de rotation principale est court, plus l'épaisseur du film est importante. Plus le temps de rotation principal augmente, plus le film devient fin. Lorsqu'elle dépasse 20 s, l'épaisseur du film reste quasiment inchangée. Par conséquent, le temps de rotation principal est généralement choisi pour être supérieur à 20 secondes. La relation entre le temps de rotation principal et l'épaisseur du film est illustrée à la figure 2.
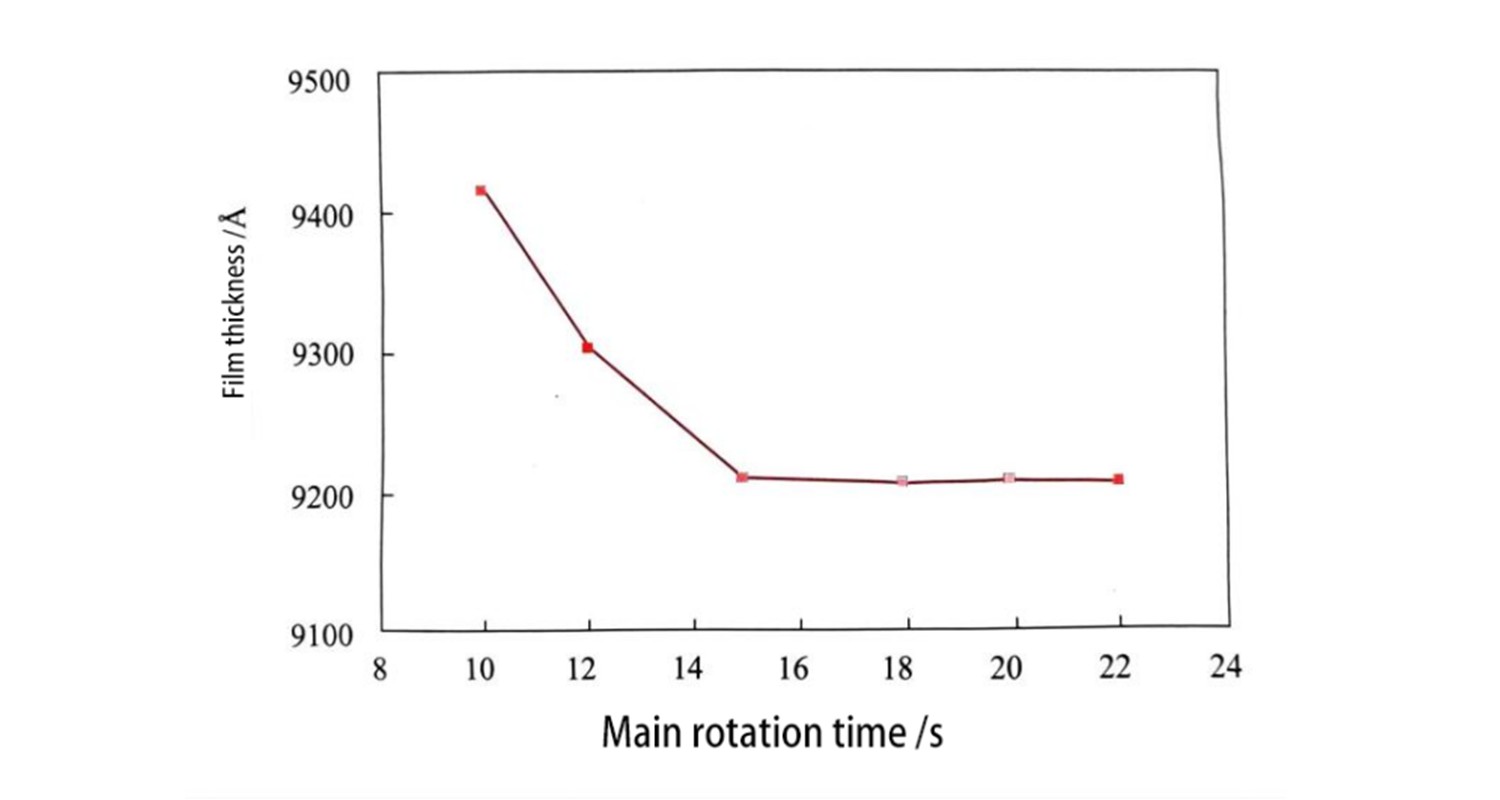
Figure 2 : Relation entre le temps de rotation principal et l'épaisseur du film
Lorsque la résine photosensible s'égoutte sur le substrat, même si la vitesse de rotation principale ultérieure est la même, la vitesse de rotation du substrat pendant l'égouttement affectera l'épaisseur finale du film. L'épaisseur du film photorésistant augmente avec l'augmentation de la vitesse de rotation du substrat pendant l'égouttage, ce qui est dû à l'influence de l'évaporation du solvant lorsque la photorésiste est dépliée après l'égouttage. La figure 3 montre la relation entre l'épaisseur du film et la vitesse de rotation principale à différentes vitesses de rotation du substrat pendant l'égouttage de la résine photosensible. On peut voir sur la figure qu'avec l'augmentation de la vitesse de rotation du substrat dégoulinant, l'épaisseur du film change plus rapidement et la différence est plus évidente dans la zone où la vitesse de rotation principale est plus faible.
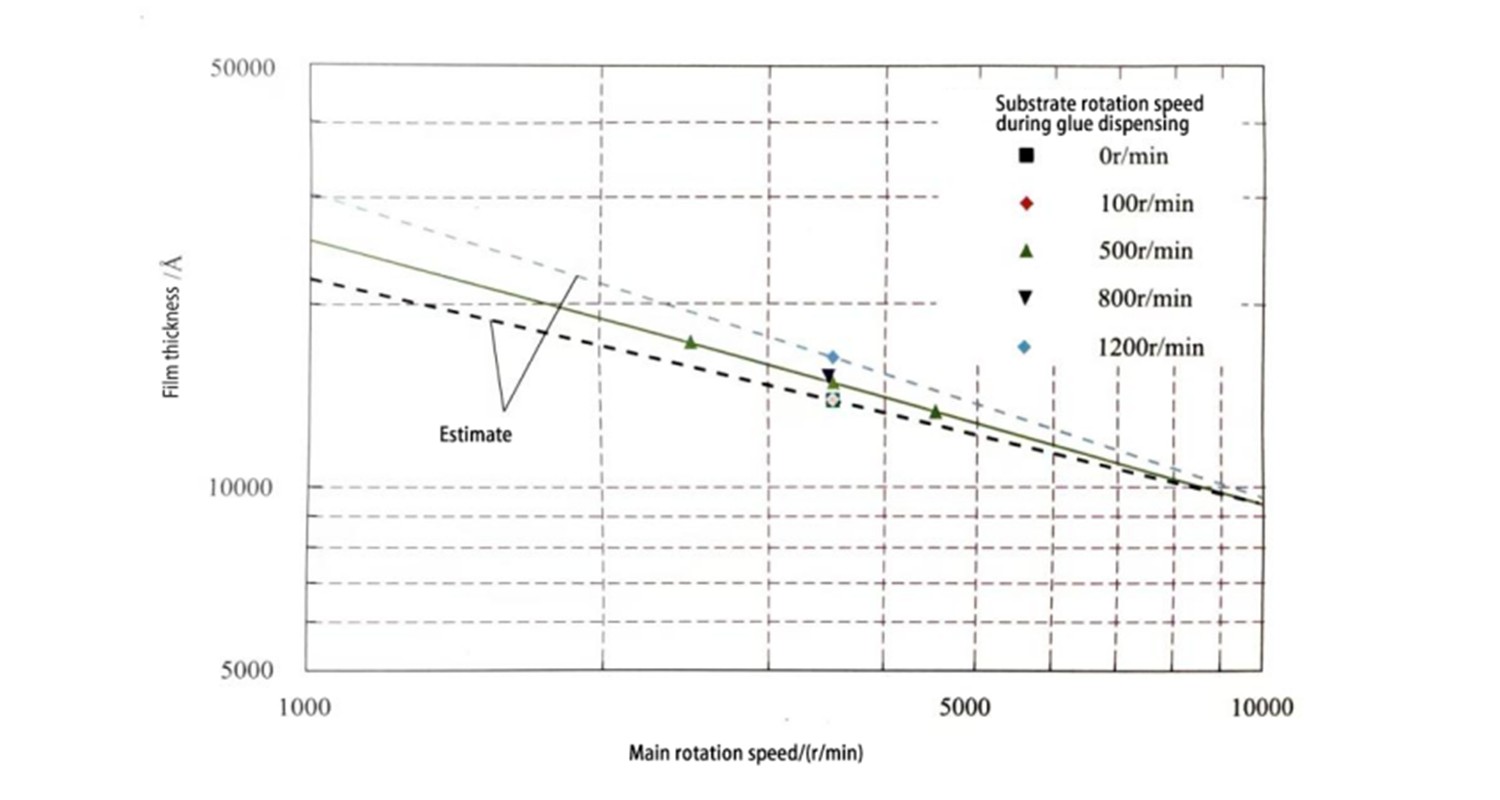
Figure 3 : Relation entre l'épaisseur du film et la vitesse de rotation principale à différentes vitesses de rotation du substrat pendant la distribution de résine photosensible
Effet de l'humidité lors du revêtement
Lorsque l’humidité diminue, l’épaisseur du film augmente, car la diminution de l’humidité favorise l’évaporation du solvant. Cependant, la répartition de l’épaisseur du film ne change pas significativement. La figure 4 montre la relation entre l'humidité et la répartition de l'épaisseur du film pendant le revêtement.
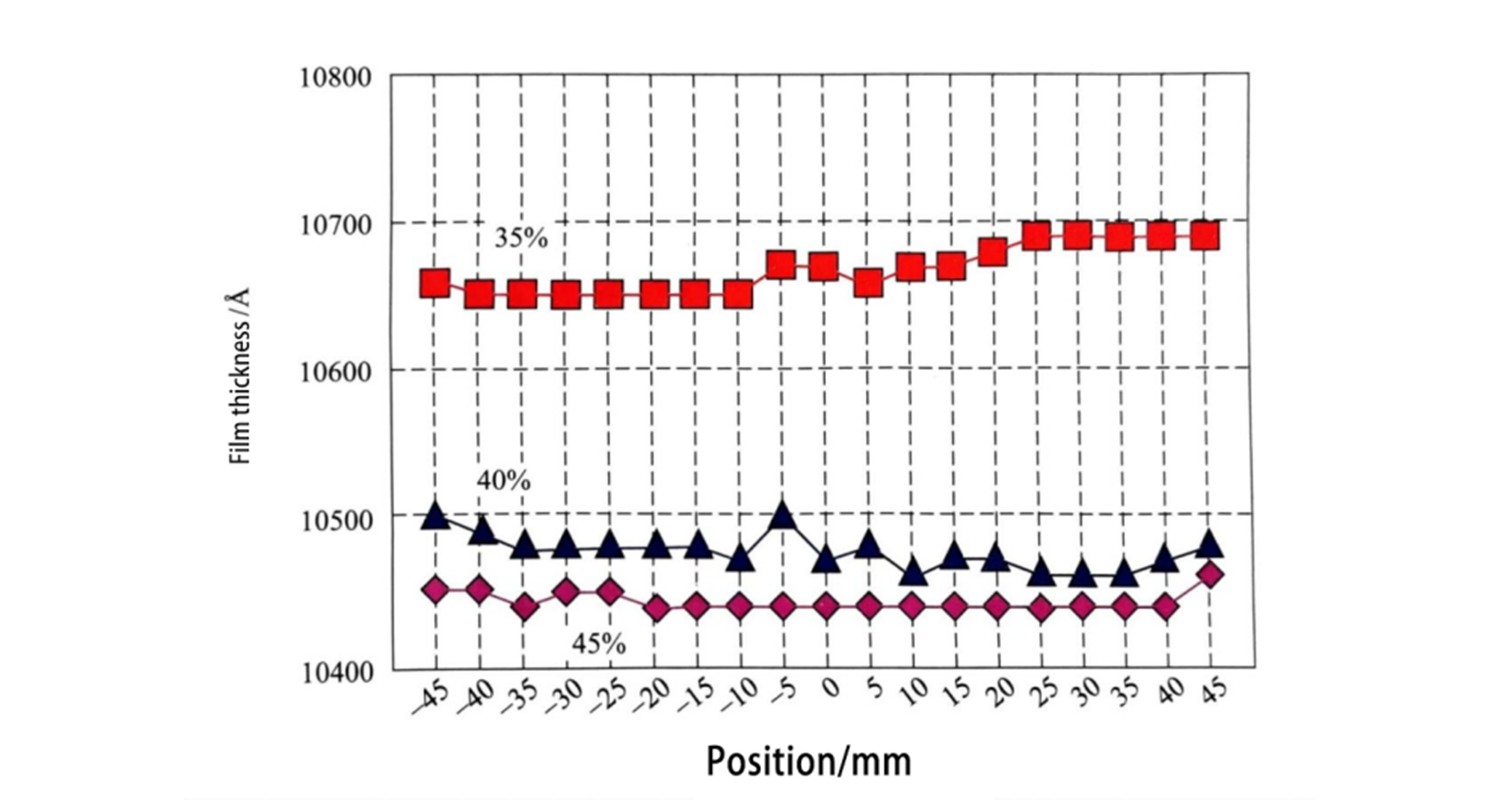
Figure 4 : Relation entre l'humidité et la répartition de l'épaisseur du film lors du revêtement
Effet de la température pendant le revêtement
Lorsque la température intérieure augmente, l’épaisseur du film augmente. On peut voir sur la figure 5 que la répartition de l'épaisseur du film photorésistant passe de convexe à concave. La courbe de la figure montre également que l'uniformité la plus élevée est obtenue lorsque la température intérieure est de 26°C et la température de la résine photosensible est de 21°C.
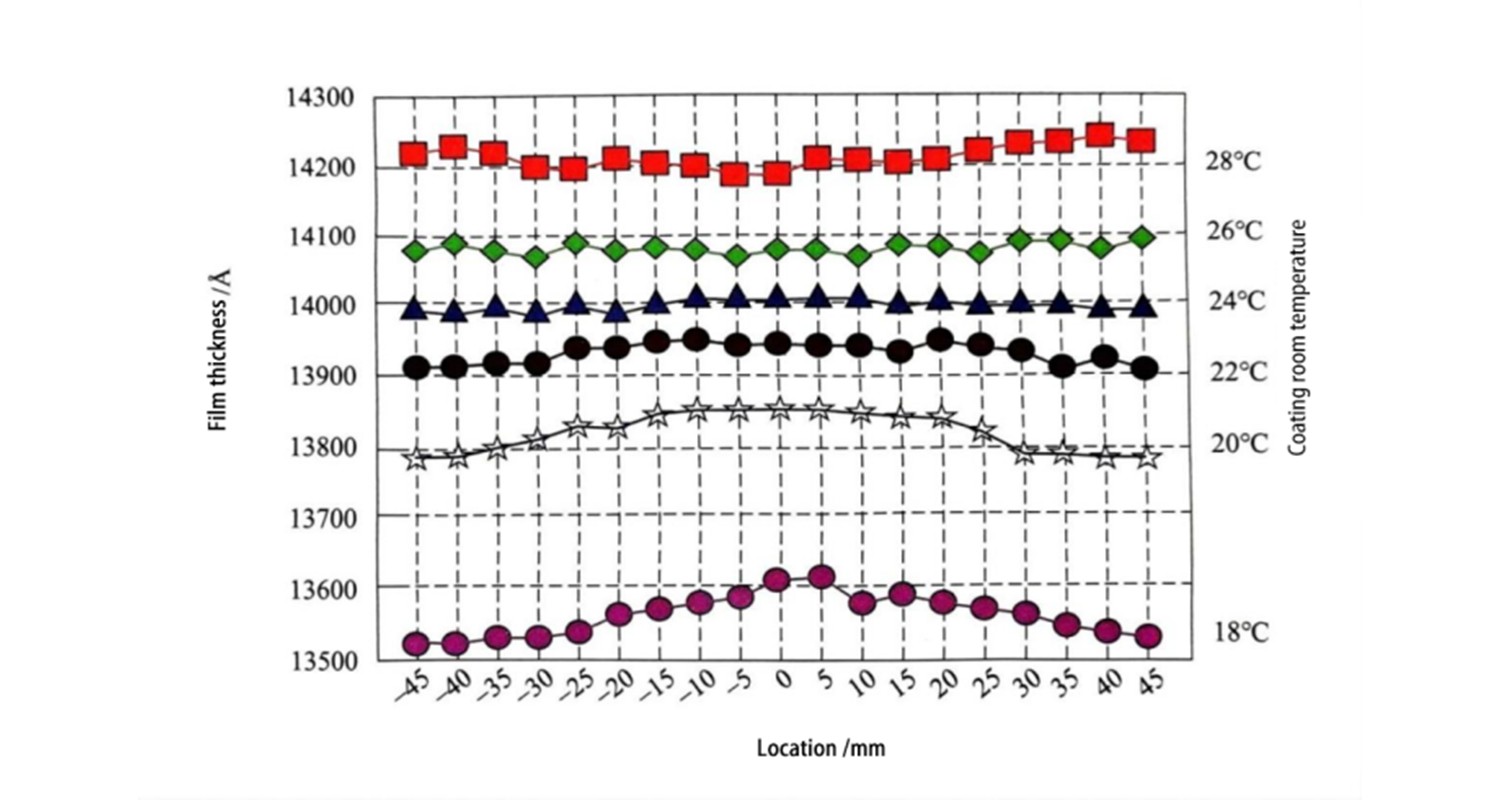
Figure 5 : Relation entre la température et la répartition de l'épaisseur du film pendant le revêtement
Effet de la vitesse d'échappement pendant le revêtement
La figure 6 montre la relation entre la vitesse d'échappement et la répartition de l'épaisseur du film. En l'absence d'échappement, cela montre que le centre de la plaquette a tendance à s'épaissir. L'augmentation de la vitesse d'échappement améliorera l'uniformité, mais si elle est trop augmentée, l'uniformité diminuera. On constate qu’il existe une valeur optimale pour la vitesse d’échappement.
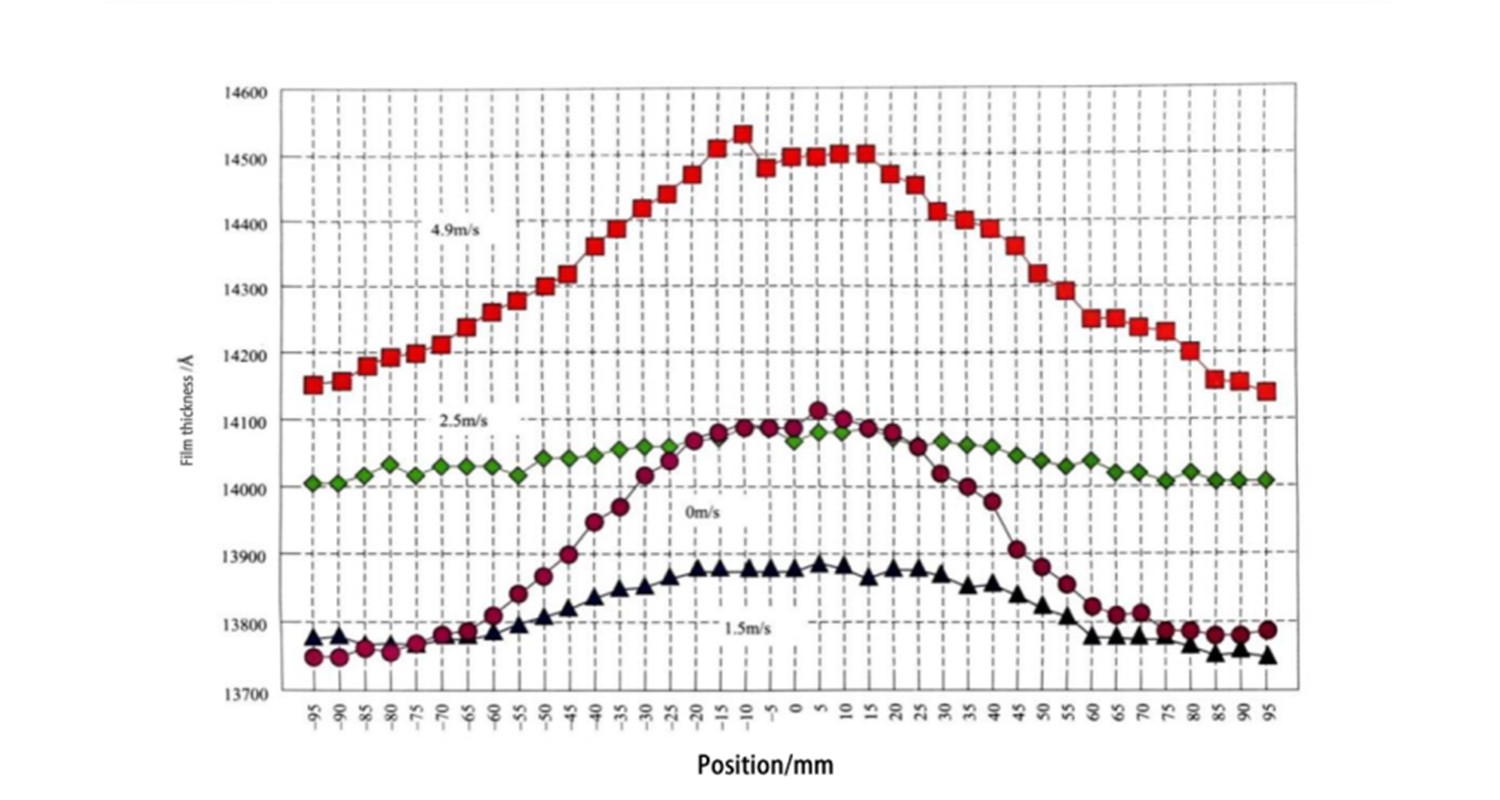
Figure 6 : Relation entre la vitesse d'échappement et la répartition de l'épaisseur du film
Traitement HMDS
Afin de rendre la résine photosensible plus facile à recouvrir, la plaquette doit être traitée avec de l'hexaméthyldisilazane (HMDS). En particulier, lorsque l'humidité est fixée à la surface du film d'oxyde de Si, du silanol se forme, ce qui réduit l'adhérence de la résine photosensible. Afin d'éliminer l'humidité et de décomposer le silanol, la plaquette est généralement chauffée à 100-120°C et un brouillard HMDS est introduit pour provoquer une réaction chimique. Le mécanisme de réaction est illustré à la figure 7. Grâce au traitement HMDS, la surface hydrophile avec un petit angle de contact devient une surface hydrophobe avec un grand angle de contact. Le chauffage de la plaquette peut obtenir une adhérence photorésistante plus élevée.
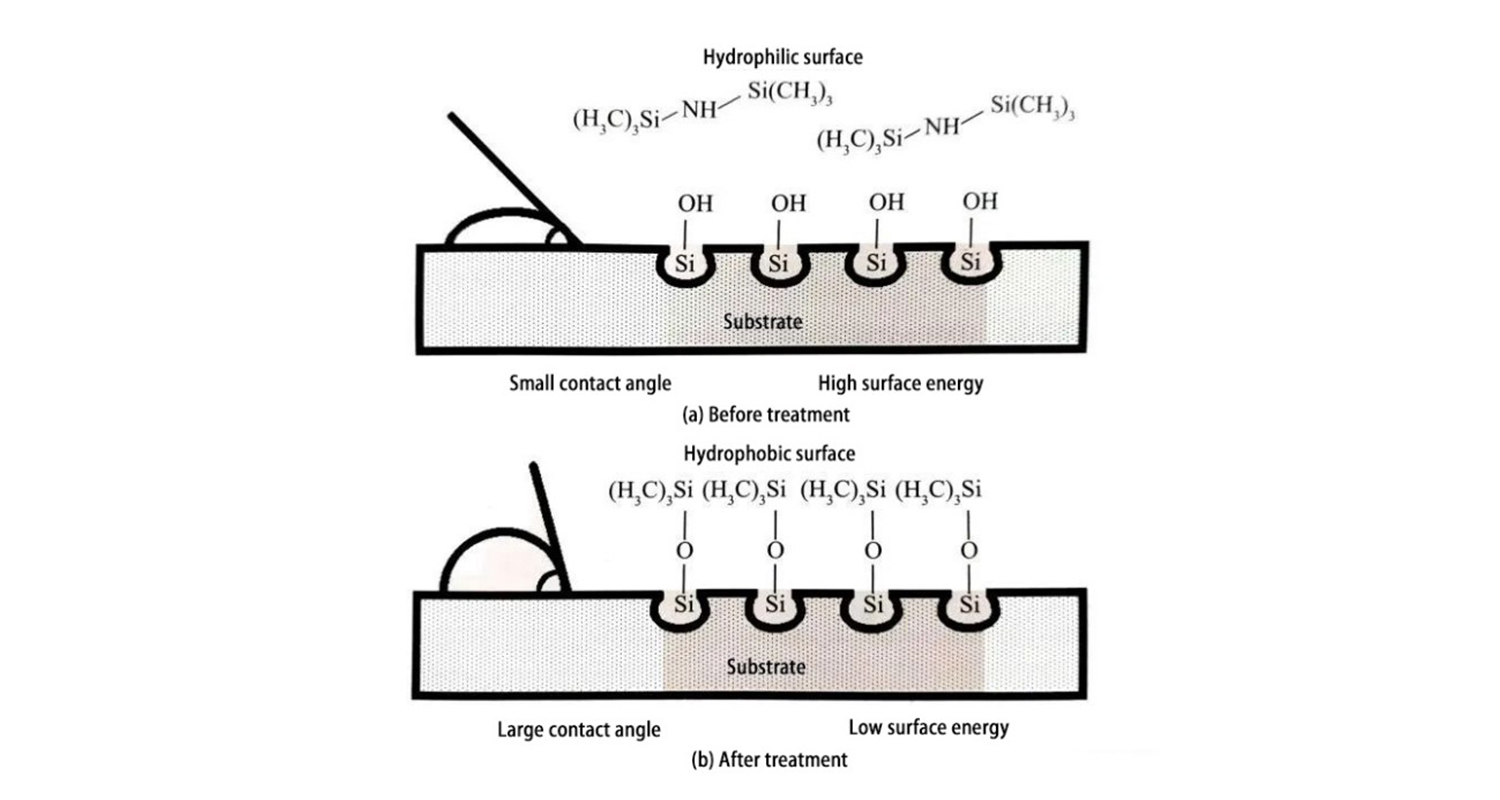
Figure 7 : Mécanisme de réaction du HMDS
L'effet du traitement HMDS peut être observé en mesurant l'angle de contact. La figure 8 montre la relation entre le temps de traitement HMDS et l'angle de contact (température de traitement 110°C). Le substrat est en Si, le temps de traitement HMDS est supérieur à 1 min, l'angle de contact est supérieur à 80° et l'effet de traitement est stable. La figure 9 montre la relation entre la température de traitement HMDS et l'angle de contact (durée de traitement 60 s). Lorsque la température dépasse 120 ℃, l'angle de contact diminue, indiquant que le HMDS se décompose sous l'effet de la chaleur. Par conséquent, le traitement HMDS est généralement effectué entre 100 et 110 ℃.
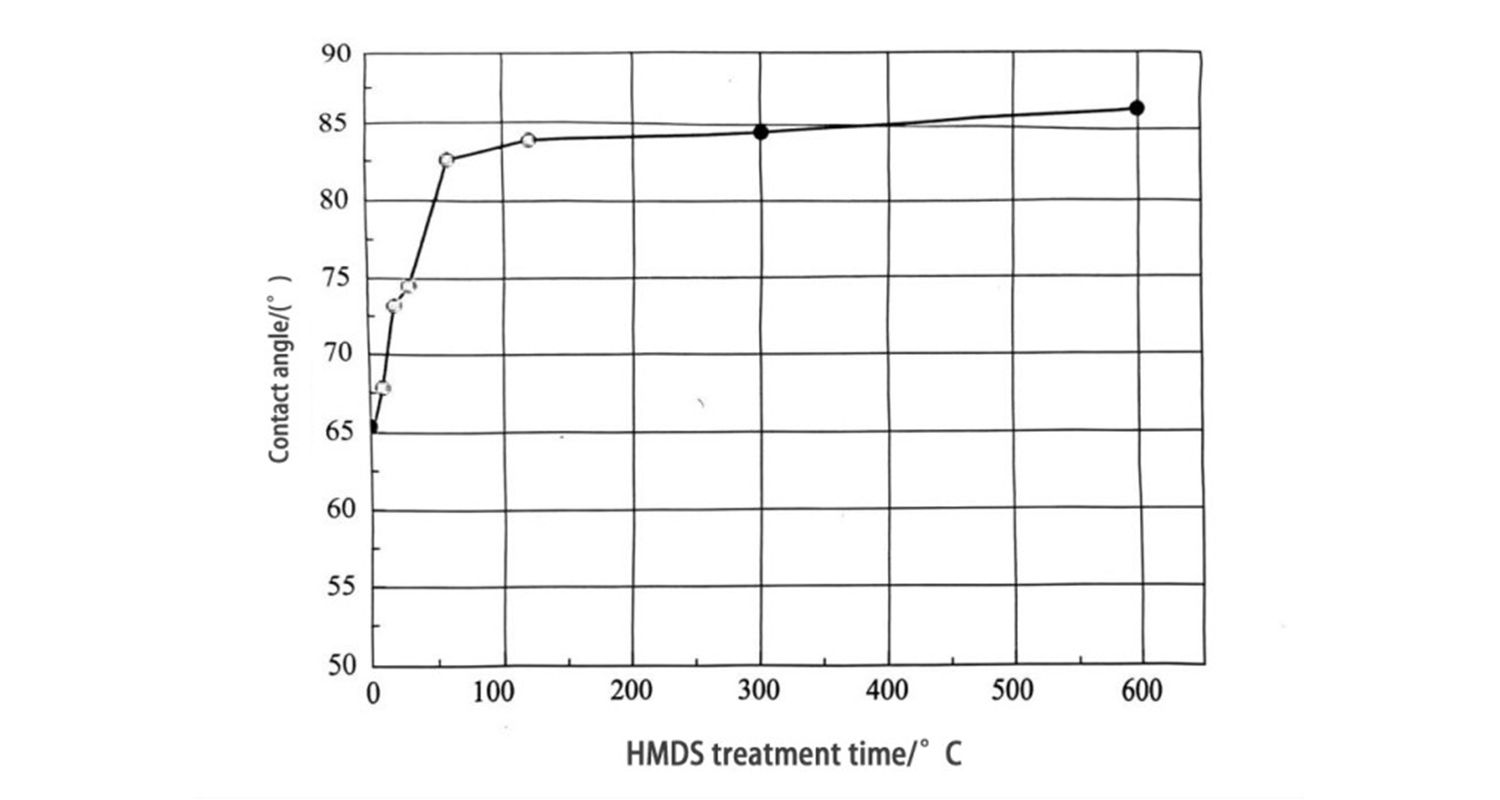
Figure 8 : Relation entre la durée du traitement HMDS
et angle de contact (température de traitement 110 ℃)
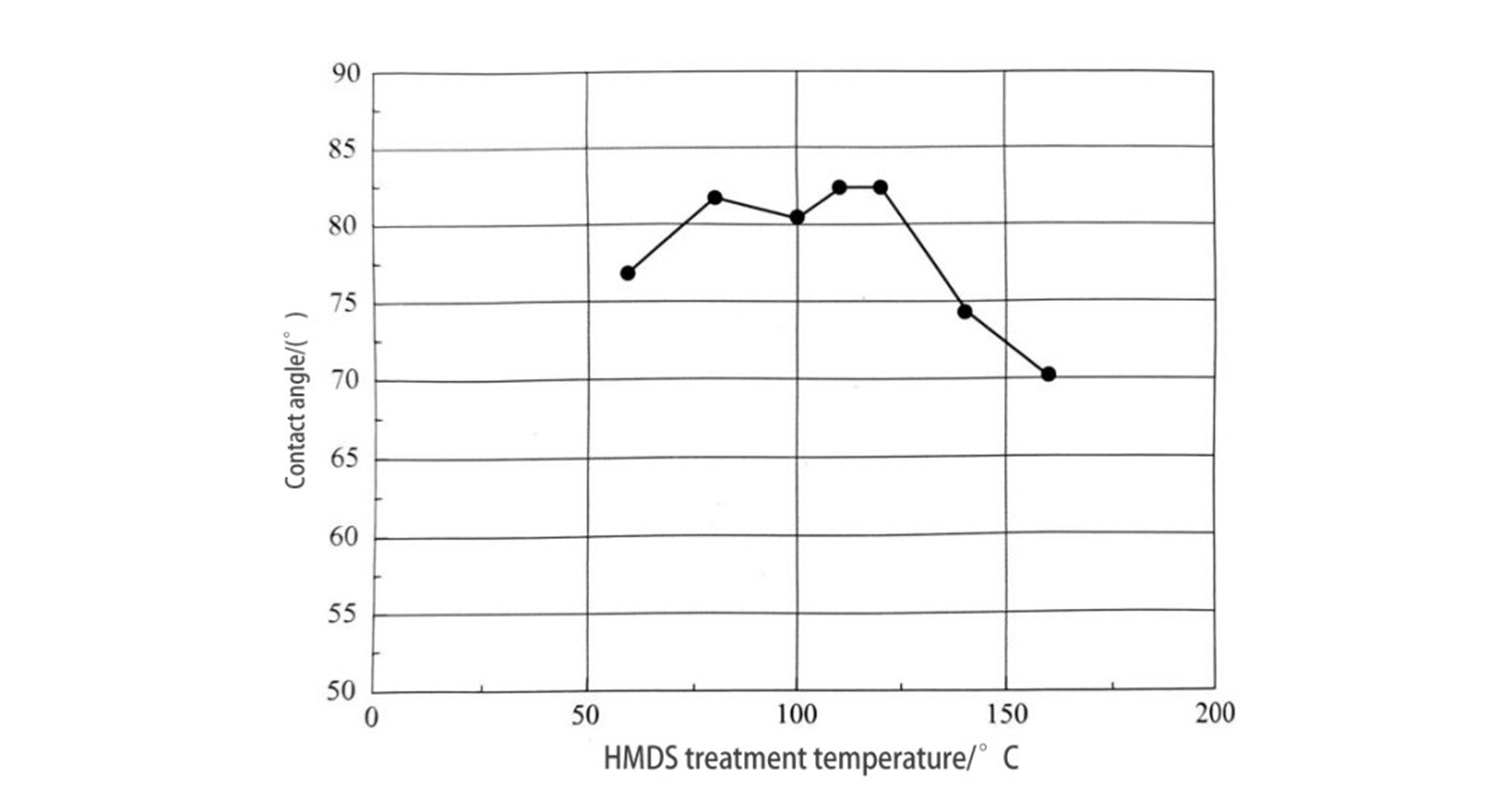
Figure 9 : Relation entre la température de traitement HMDS et l'angle de contact (durée de traitement 60 s)
Le traitement HMDS est effectué sur un substrat de silicium avec un film d'oxyde pour former un motif photorésistant. Le film d'oxyde est ensuite gravé avec de l'acide fluorhydrique avec un tampon ajouté, et il s'avère qu'après le traitement HMDS, le motif de photorésist peut être empêché de tomber. La figure 10 montre l'effet du traitement HMDS (la taille du motif est de 1 µm).
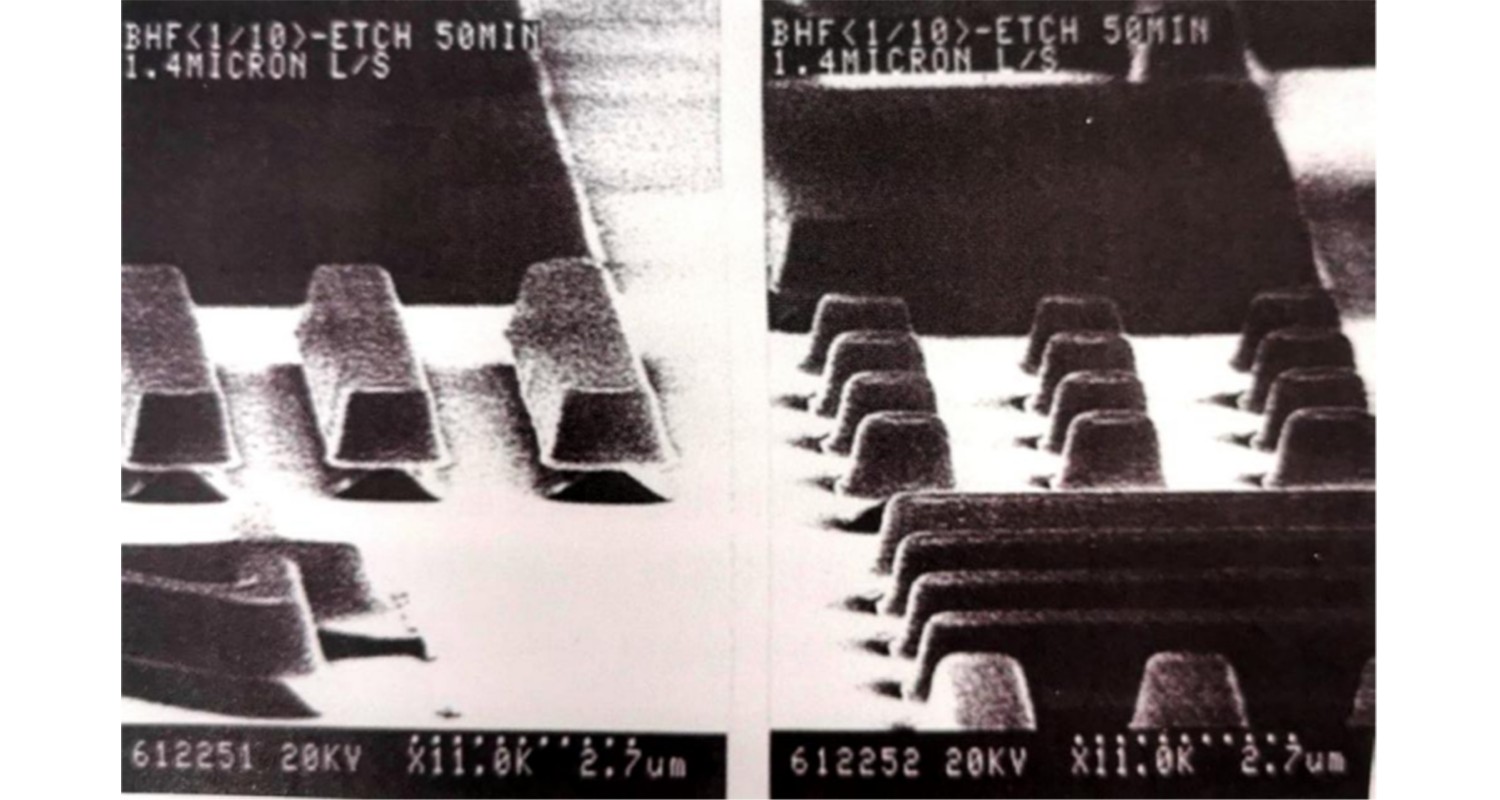
Figure 10 : Effet du traitement HMDS (la taille du motif est de 1 um)
Précuisson
À la même vitesse de rotation, plus la température de précuisson est élevée, plus l'épaisseur du film est faible, ce qui indique que plus la température de précuisson est élevée, plus le solvant s'évapore, ce qui entraîne une épaisseur de film plus fine. La figure 11 montre la relation entre la température de précuisson et le paramètre A de l'aneth. Le paramètre A indique la concentration de l'agent photosensible. Comme le montre la figure, lorsque la température de précuisson s'élève au-dessus de 140°C, le paramètre A diminue, indiquant que l'agent photosensible se décompose à une température supérieure à celle-ci. La figure 12 montre la transmission spectrale à différentes températures de pré-cuisson. À 160°C et 180°C, une augmentation de la transmission peut être observée dans la plage de longueurs d'onde de 300 à 500 nm. Cela confirme que l'agent photosensible est cuit et décomposé à haute température. La température de précuisson a une valeur optimale, qui est déterminée par les caractéristiques de la lumière et la sensibilité.
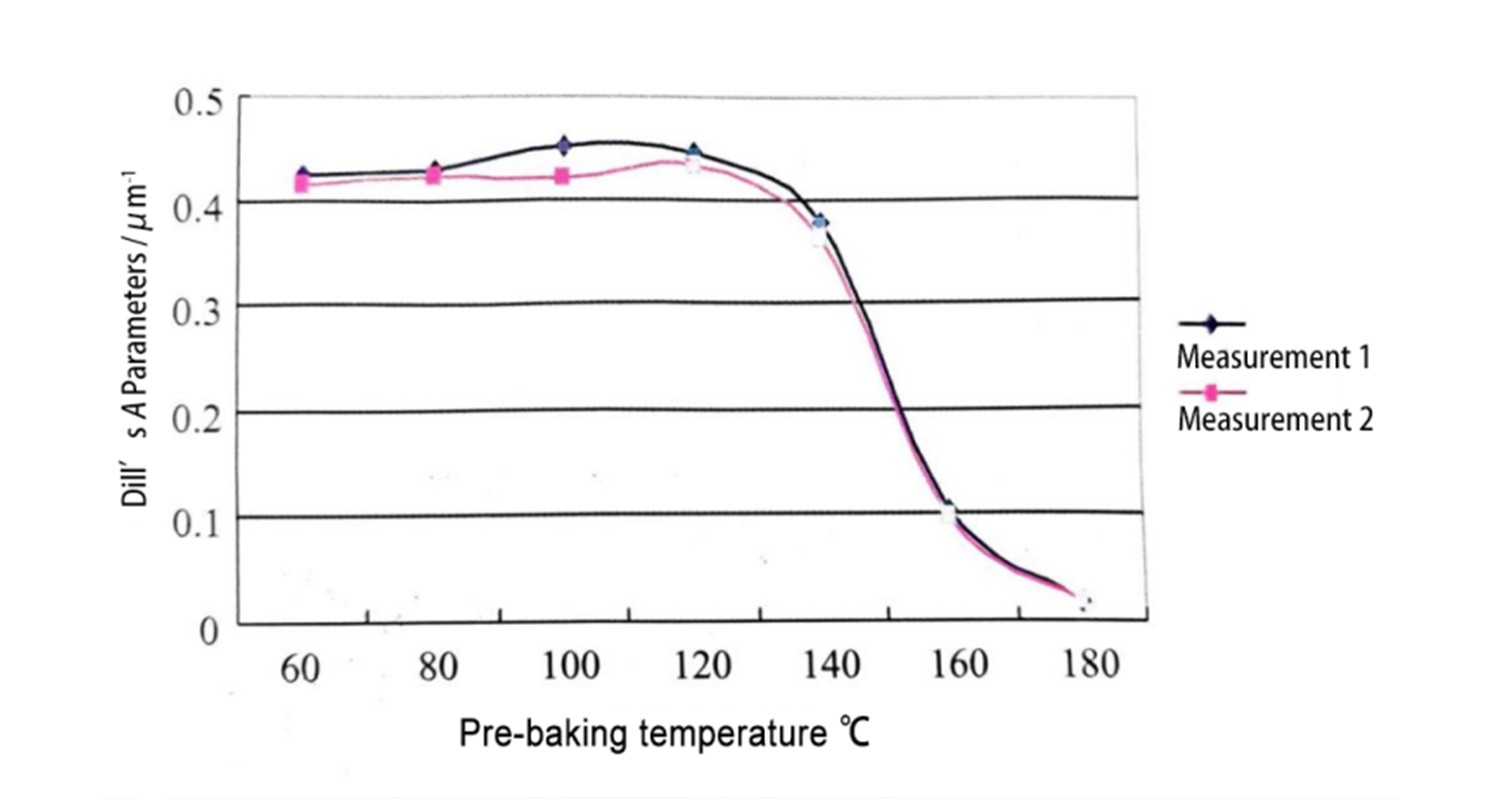
Figure 11 : Relation entre la température de précuisson et le paramètre A de l'aneth
(valeur mesurée de OFPR-800/2)
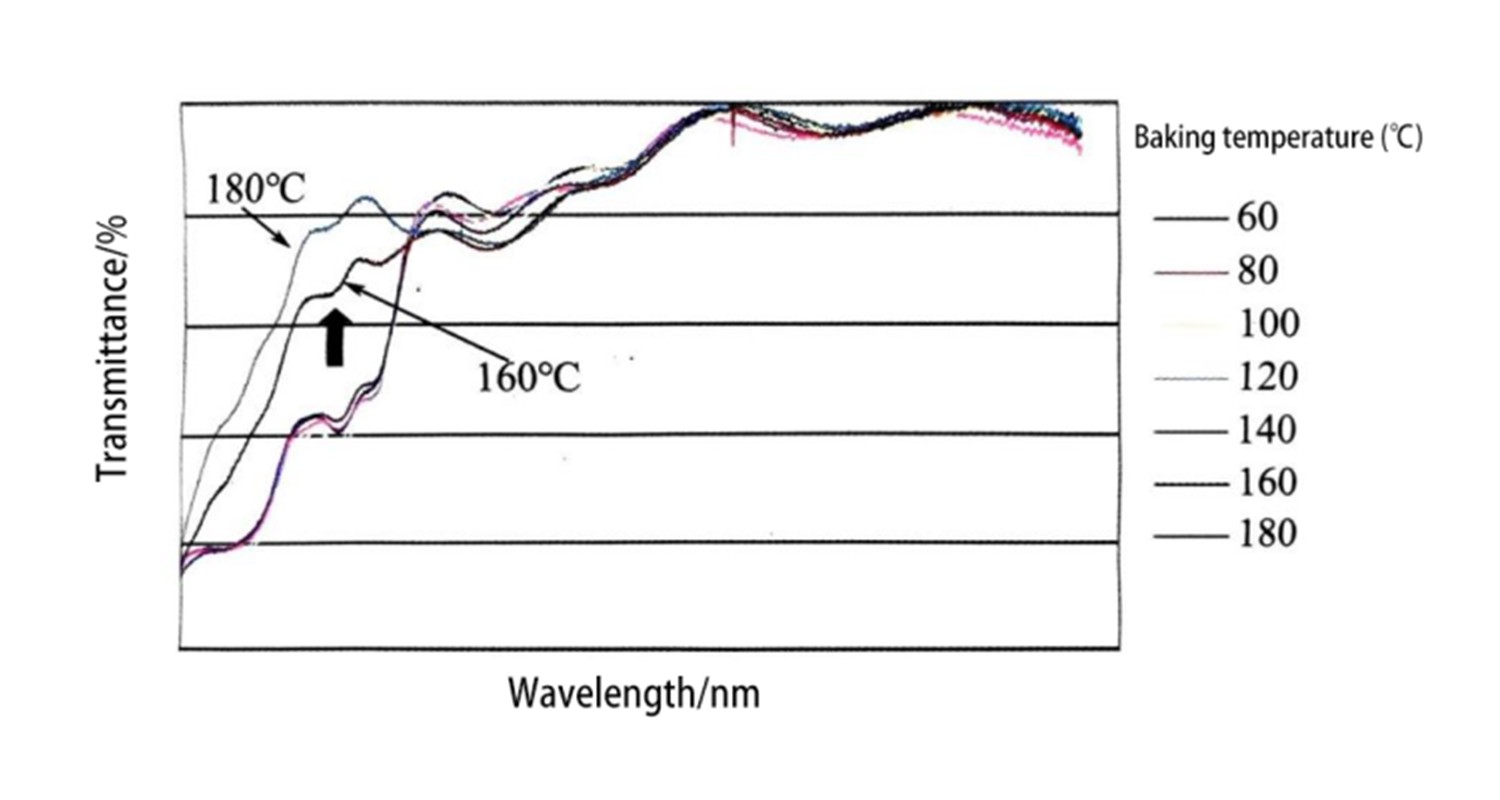
Figure 12 : Transmission spectrale à différentes températures de précuisson
(OFPR-800, épaisseur de film 1um)
En bref, la méthode de revêtement par centrifugation présente des avantages uniques tels qu'un contrôle précis de l'épaisseur du film, des performances en termes de coûts élevés, des conditions de traitement douces et un fonctionnement simple, de sorte qu'elle a des effets significatifs sur la réduction de la pollution, les économies d'énergie et l'amélioration des performances en termes de coûts. Ces dernières années, le revêtement par centrifugation a fait l’objet d’une attention croissante et ses applications se sont progressivement étendues à divers domaines.
Heure de publication : 27 novembre 2024